
ORDERS:
704-799-2192

BIKE SPECIFIC
PARTS PAGES
FOR NEW
'03-'22 Models
(Grom, Monkey
Z125, RC390,
R3, R1, R6,
ZX-10, ZX6
CBR's, GSX-R's
& more)

"VIC" Repeat
Customer Discount
Program
TOP SELLERS

Ohlins Shocks,
Forks, & Dampers

Antigravity
Superlight
Lithium Batteries
PRODUCT CATEGORIES
Air Filters
Alarms
Apparel
Batteries
Bodywork
Brakes
Cameras
Carburetors
Cargo Racks
Chains / Sprockets
Chain Adjusters
Clip-ons
Clutches
Controls
Gauges / Dash
Electronics
Engine Covers
Engine Parts
Exhaust
Fairing Stay
Fender
Eliminators
Fenders / Huggers
Fuel Caps / Bases
Fuel Injection
GS911
Service Tool
Hard Parts
Head Set
Communications
Helmets
H.I.D & LED
Head Lights
Lap Timers
Levers
Mirrors / Mirror Block Off Plates
Nitrous
Oil Filters
Protection / Frame Sliders
Quick Shifters
Race Stands
Radar Detectors
Radiator Hose Kits
Rear Sets / Foot Controls
Seats / Seat Cowls
Slipper Clutch
Speedo Tuner
Sprockets / Chains
Steering Dampers
Sunglasses
Suspension
Tail Lights
Tank
Traction Pads / Stomp Grip
Throttle Kits
Throttle Lock / Cruise Control
Tires
Tire Warmers
Tire Pressure Monitoring (TPMS)
Under Tails
Velocity
Stacks
Wheels
Windscreens
Zombie Target
NecksGen
"VIC" Repeat
Customer Discount
Program

| |
 |
CAN YOU
REALLY TELL
AN AKRAPOVIC FROM OTHER EXHAUST SYSTEMS? |
How to
recognize the essential elements of a good exhaust system
|
In our years of experience on the aftermarket
exhaust components market and encounters with the competition, we have
gained a great deal of knowledge. There is a surprising number of
exhaust system manufacturers whose products vary widely in terms of
development and quality. Even with a quick glance we can distinguish a
high-quality and successful manufacturer from one who is following the
trend-setters in any way they can. We find it troubling that some of
these manufacturers pay little attention to the quality of their
products, and therefore to their customers and their safety.
We come across various types of exhaust systems every day. We can
say that some of them are good and some are bad, especially after a
detailed inspection of design deficiencies and production quality.
For this reason, as one of the leading designers and manufacturers of
high-performance exhaust systems, in keeping with the philosophy of our
company, the reputation of the Akrapovic brand and our experiences in
the field of motorcycle racing, we feel obliged to draw your attention
to certain important factors which influence the durability, safety and
operation of high-performance exhaust systems.
In order to make a clear demonstration of these factors we have selected
an exceptionally good example of a competitor’s product and compared it
with our exhaust system, since this is the only way to make a detailed
comparison of the differences and support our introductory statement
about high-quality and lower quality exhaust systems. We would like to
illustrate certain differences which an attentive potential customer or
even a dealer might not notice, and which are reflected on the product
itself as deficiencies which have a major effect on the safety and
durability of the system. Obviously, on a poor system such deficiencies
are apparent at first glance.
We compared a competitor’s full titanium exhaust system for the
ZX 10 R 04-05
with an Akrapovic Evolution exhaust system – product code S-K10RFT2TL-T,
whose characteristics and design are similar to the competitor’s system.
We will begin the comparison with the input end of the system – the
header tubes, and end with the specific characteristics of the material
used by Akrapovic to produce our top product line, the Evolution.
Through this comparison we wish to inform potential customers about how
to make a good assessment of the product they want to purchase, and at
the same time to respond to the question of why Akrapovic exhaust
systems are so highly rated by enthusiasts, i.e. where the added value
lies which separates good exhaust systems from bad ones.
|
 |
 |
COMPETITION |
|
AKRAPOVIC |
HEADER TUBES |
|
|
|
|
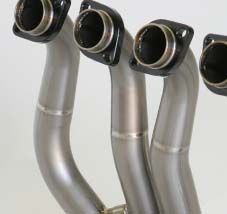 |
|
 |
|
|
Akrapovic
header tubes together with conical elements made using the hydroforming
process, with which we ensure the optimal flow of the exhaust gases,
i.e. minimize the negative turbulence of the gases. |
|
|
|
 |
|
 |
No
springs to attach header tubes to the head of the engine:
- header tube
inner sleeves are welded to the header tubes and do not allow the
flanges to be removed from the header tubes. This means that the inner
sleeve, header tube and flange cannot be separated. Since the header
tubes are attached via the flanges directly to the head, the header
tubes cannot be removed quickly.
- this type
of attachment causes engine vibrations to be transferred directly to the
material and welds of the exhaust system (increased material stress). |
|
Inner
sleeves, flanges and header tubes are independent. Therefore the header
tubes are “free-floating”, and are attached to the engine head using
springs. They are not bolted in. Only the flanges are screwed in, and
these hold the inner sleeves. This system allows faster removal and
installation of the header tubes in racing situations. Stress on the
material due to engine vibration is reduced to a minimum. |
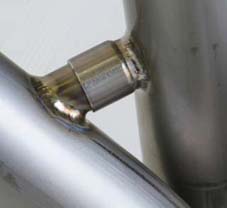 |
|
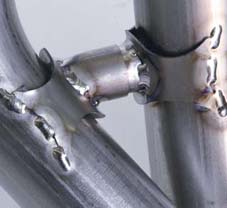 |
Interference crossover tubes are made
without reinforcement, which due to the use of titanium could result in
cracking of the joints. |
|
Due to our
experience, we always reinforce our titanium interference crossover
tubes. |
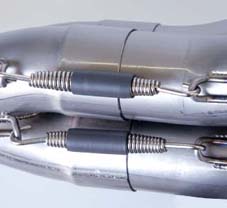 |
|
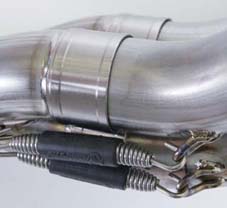 |
All joints on the individual components
are made by expanding the material and not with CNC machined sleeves.
The expanded joints gradually become stressed and crack – the material
becomes worn. This approach significantly reduces the compactness of the
configuration, i.e. allows unwanted play in the joints, thus allowing
the individual system components to move. |
|
The joints
between individual components are made from CNC machined sleeves. Only
in this way, using allowable tolerances, can we ensure constant precise
contact between individual components and permanent compactness of the
system. |
|
|
EYE LETS |
|
|
|
|
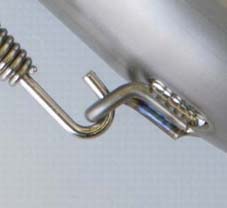 |
|
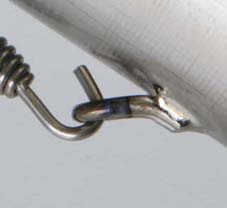 |
Eyelets for attaching the springs are made
out of too-thin material. The spring gradually cuts through the material
and wears out the eyelet at the contact point. |
|
We use
a special type of titanium which is not subject to the mechanical
influences of the steel springs. |
|
|
|
MUFFLER |
|
|
|
|
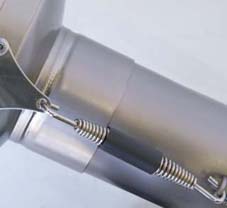 |
|
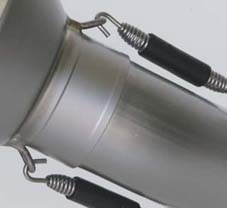 |
The opening
on the inlet cap of the muffler (muffler – link pipe joint) is again
made using expansion (see HEADER TUBES) |
|
The opening
on the inlet cap of the muffler (muffler – link pipe joint) is, like all
our joints between individual components (header tubes – collector –
link pipe) made from a CNC machined sleeve.
|
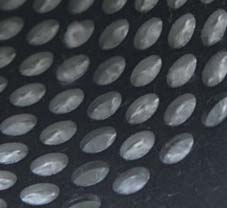 |
|
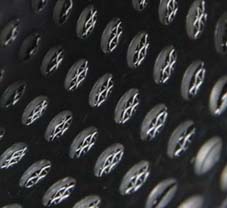 |
The interior packing of the muffler is
damping wool (E-glass). It lacks additional protection against strong
engine pulses, which leads to faster wearing out of the muffler packing. |
|
In addition to the damping wool, the
interior of the muffler contains an SS mesh/SS wool/SS mesh sandwich,
which prevents excessive combustion of the muffler packing material
under heavier loading. |
|
|
MUFFLER CLAMP & BRACKET |
|
|
|
|
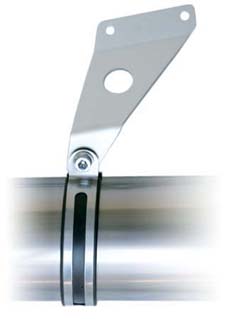 |
|
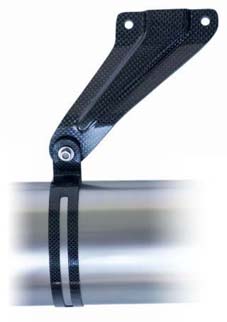 |
Muffler clamp
made of cheap stamped stainless steel with a rubber washer. The rubber
in this case acts as an insulator, which can lead to an unwanted effect
– local overheating of the muffler (at the point where the washer
touches muffler the outer sleeve). Muffler bracket made of aluminum. |
|
To attach the Akrapovic muffler to the
motorcycle frame we use an in-house developed carbon-fiber clamp and
carbon-fiber bracket. With the use of this material we avoid local
overheating of the muffler outer sleeve, and due to the flexibility of
the clamp and bracket the vibrations of the frame and the exhaust
system are sufficiently damped. The low weight of carbon fiber lowers
the overall weight of the system. |
|
|
|
WELDING AND STRUCTURE OF INDIVIDUAL
PARTS OF TUBES |
|
|
|
|
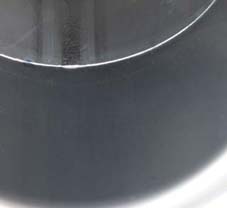 |
|
 |
Irregularities in the welds in certain
parts of the component: insufficient reheating and fusing of the
materials – a weld which looks good on the outside does not guarantee
hardness, soundness and therefore safety. |
|
The perfect fit of individual tube parts
around their circumference is extremely important, since this makes
accurate welding possible only where it is needed. We avoid weld leakage
into the interior of the tube, which acts like an unwanted scar on the
interior tube surface, disrupting the smooth flow of exhaust gases and
distorting the system’s performance characteristics. |
|
|
|
MATERIAL |
|
|
|
|
|
|
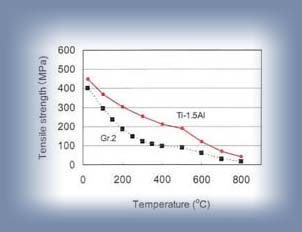 |
The system we obtained uses grade 1 or
grade 2 titanium, i.e. so-called commercial pure titanium, which does
not satisfy all of the stress conditions which appear during the
operation of the exhaust system. Grade 1 or grade 2 titanium is not
sufficiently temperature resistant, as it tolerates temperatures only up
to 300º - 400ºC. The temperature of exhaust gases when exiting the
engine head can reach up to 800ºC. |
|
Akrapovic uses a special type of titanium for its Evolution exhaust
systems. On the basis of an exclusive contract with Japanese
manufacturer Kobe Steel, we have a concession for a special titanium
alloy intended exclusively for the production of Akrapovic exhaust
systems. This alloy conforms to grade 3 level of tensile strength and
resistance to oxidation at high temperatures. According to
specifications, at 800ºC this alloy must tolerate one level of tensile
strength higher than grade 2 titanium. At temperatures between 200 and
500 ºC it must demonstrate up to 3x higher strength (red line).
This
alloy also responds very well to forming and is easy to weld. |
|